Aluminum PCBs
Among all Metal core PCBs, Aluminum PCB is the most common type. The base material consists of an aluminum core and standard FR4. It features a thermal clad layer that dissipates heat in a highly efficient manner while cooling components and increasing the overall performance of the products. Currently, Aluminum Backed PCB is regarded as the solution to high power and tight tolerance applications.
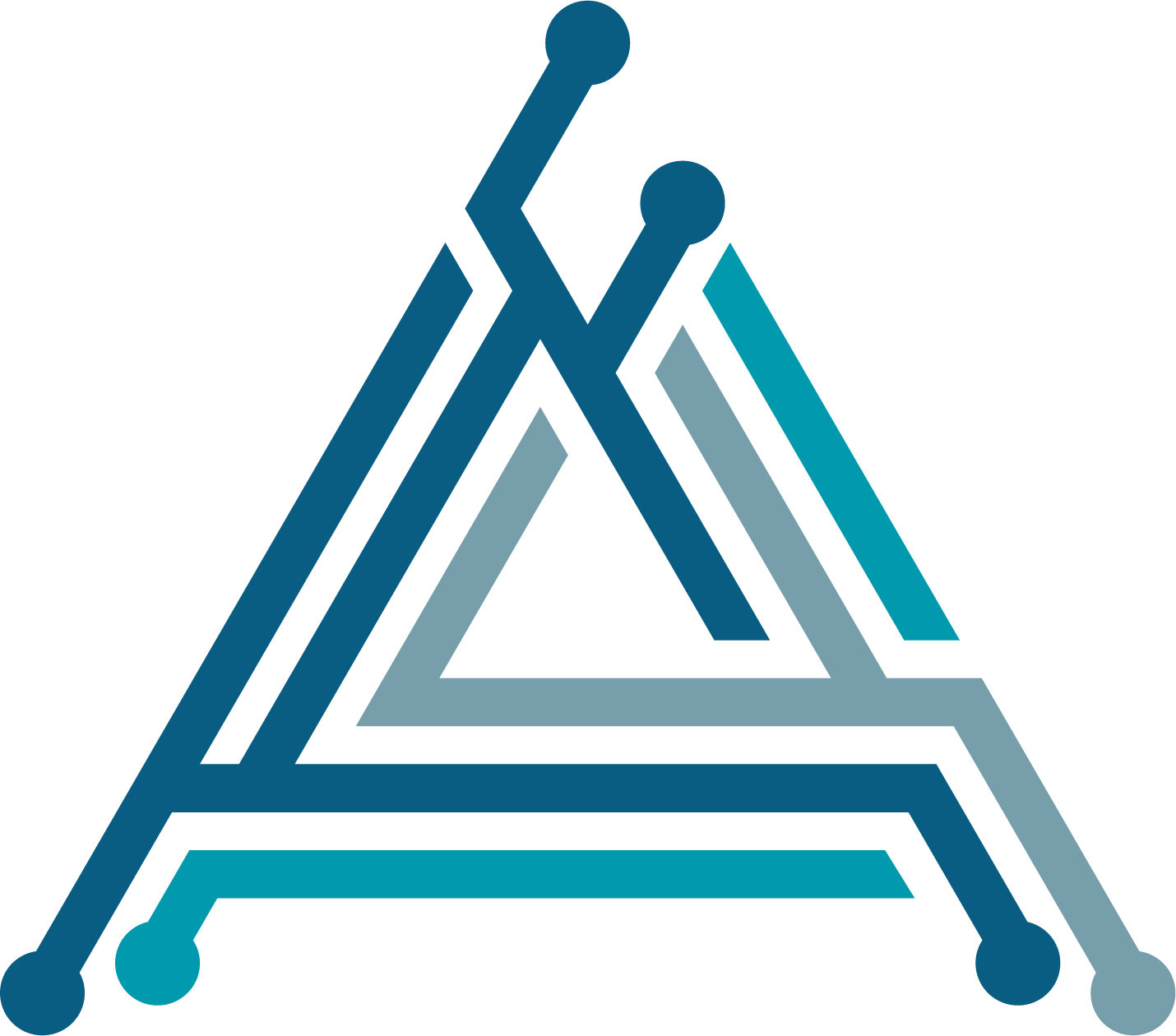
General Introduction of Aluminum PCB
Among all Metal core PCBs, Aluminum PCB is the most common type. The base material consists of an aluminum core and standard FR4. It features a thermal clad layer that dissipates heat in a highly efficient manner while cooling components and increasing the overall performance of the products. Currently, Aluminum Backed PCB is regarded as the solution to high power and tight tolerance applications.
Structure of Aluminum PCB
Circuit Copper Layer
The circuit copper layer (usually using electrolytic copper foil) is etched to form a printed circuit, which is used to realize the assembly and connection of the device. Compared with the traditional FR-4, with the same thickness and the same line width, the aluminum substrate can carry a higher current.
Advantages of Aluminum PCB
Environmentally Friendly: Aluminum is non-toxic and recyclable. Manufacturing with aluminum is also conducive to conserving energy due to its ease of assembly. For printed circuit board suppliers, using this metal helps maintain the health of our planet.
Heat dissipation:
High temperatures can cause severe damage to electronics, so it is wise to use a material that can help dissipate heat. Aluminum can actually transfer heat away from vital components, thus minimizing the harmful effect it could have on the circuit board.
Higher durability:
Aluminum provides strength and durability to a product that ceramic or fiberglass bases cannot. Aluminum is a sturdy base material that can reduce accidental breakage during manufacturing, handling, and everyday use.
Lightweight:
For its incredible durability, aluminum is a surprisingly lightweight metal. Aluminum adds strength and resilience without adding on any additional weight.
Insulating Layer
The insulating layer is the core technology of the aluminum substrate, which mainly plays the functions of bonding, insulation and heat conduction. The aluminum substrate insulating layer is the largest thermal barrier in the power module structure.
The better the thermal conductivity of the insulating layer, the more favorable it is to spread the heat generated during the operation of the device, and the lower the operating temperature of the device, so as to increase the power load of the module, reduce the volume, extend the life-span, and increase the power output .
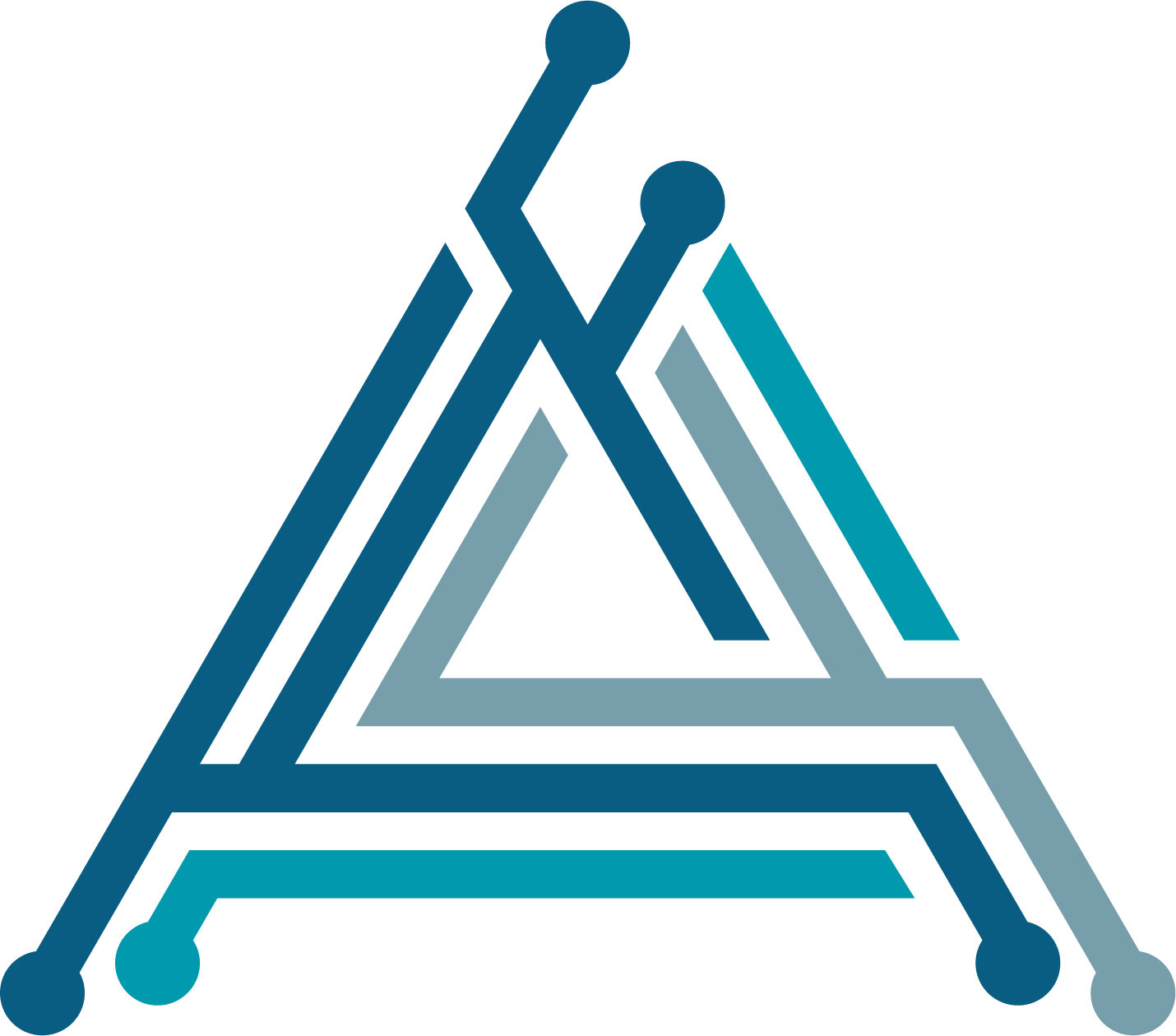
Metal substrate
What kind of metal is used for the insulating metal substrate depends on the comprehensive consideration of the thermal expansion coefficient, thermal conductivity, strength, hardness, weight, surface state and cost of the metal substrate.
In general, considering the conditions such as cost and technical performance, aluminum plate is an ideal choice. Available aluminum plates are 6061, 5052, 1060 and so on. If there are higher requirements for thermal conductivity, mechanical properties, electrical properties and other special properties, copper plates, stainless steel plates, iron plates and silicon steel plates can also be used.
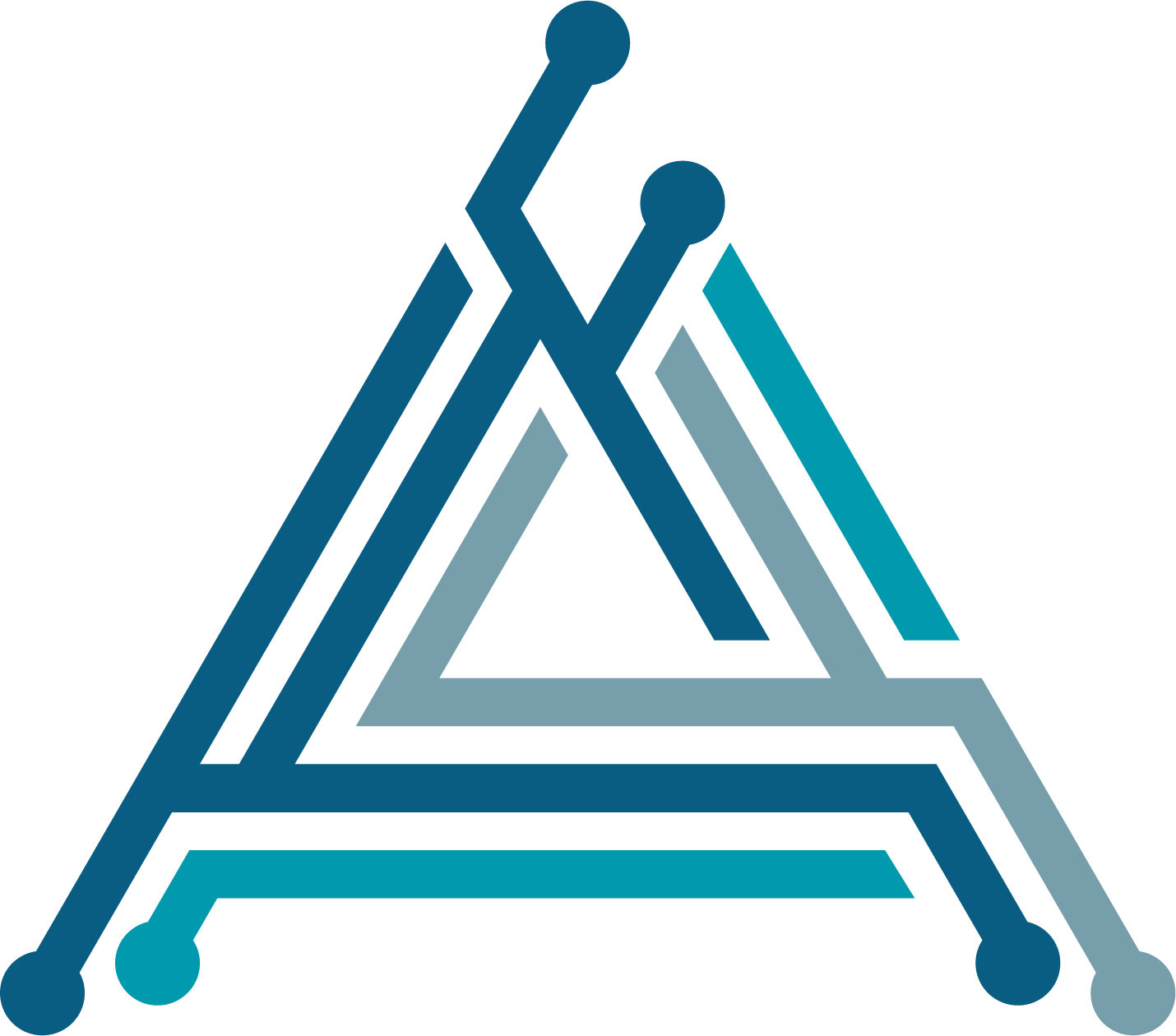
Application of Aluminum PCB
Audio device
Input, output amplifier, balanced amplifier, audio amplifier, pre-amplifier, power amplifier.
Communication electronic equipment
High-frequency amplifier, filtering appliances, the transmitter circuit
Power Supply
Switching regulator, DC / AC converter, SW regulator, etc.
Office automation equipment
Motor drive, etc.
Automobile
Electronic regulator, ignition, power supply controller, etc.
Computer
CPU board, floppy disk drive, power supply devices, etc.
Power Modules
Inverter, solid-state relays, rectifier bridges.
Lamps and lighting
As the advocated promotion of energy-saving lamps, a variety of colorful energy-saving LED lights are well received by the market, and aluminum PCB used in LED lights also begin large-scale applications.
Storage conditions
Aluminum PCBs are generally stored in a dark, dry environment. Most aluminum PCBs are prone to moisture, yellowing, and blackening. Generally, they should be used within 48 hours after opening the vacuum package.
Aluminium layer thickness
2 layers aluminum PCB substrate, copper thickness 1oz, aluminum base on the bottom of the laminate is probably like this for reference. The above parameters are basically unchanged.
Check AlteraFlex Aluminum core PCB manufacturing capabilities in the following table:
Feature | Capability |
---|---|
Material | Aluminum core (Domestic 1060), Copper core, FR4 covering |
Thermal conductivity | 1.0W/(m*k),2.0W/(m*k) |
Min. Track/Spacing | 4mil |
Min. Hole Size | 0.8mm |
Base Material | Aluminum, FR4, Flex, Flex-rigid, HDI, Rogers, etc. |
Board Thickness | 0.4-3.2mm |
Surface Finishing | Immersion gold, OSP, Hard Gold,Immersion SIlver,Enepig |
Finsih Cooper | 1-4oz |
Solder Mask | Green, Red, Yellow, Blue, White, Black, Purple, Matte Black, Matte green |
Silkscreen | White, Black |
Via Process | Tenting Vias,Plugged Vias,Vias not covered |
Testing | Fly Probe Testing (Free) and A.O.I. testing |
Build time | 2-3 days |
lead time | 2-3 days |
Have Questions?
If you have any questions or need any further information, please feel free to contact your dedicated customer service.