AlteraFlex Circuits PCB Capabilities
AlteraFlex Circuits is a professional quick-turn PCB prototyping, PCB Assembly, and low-volume production manufacturer.
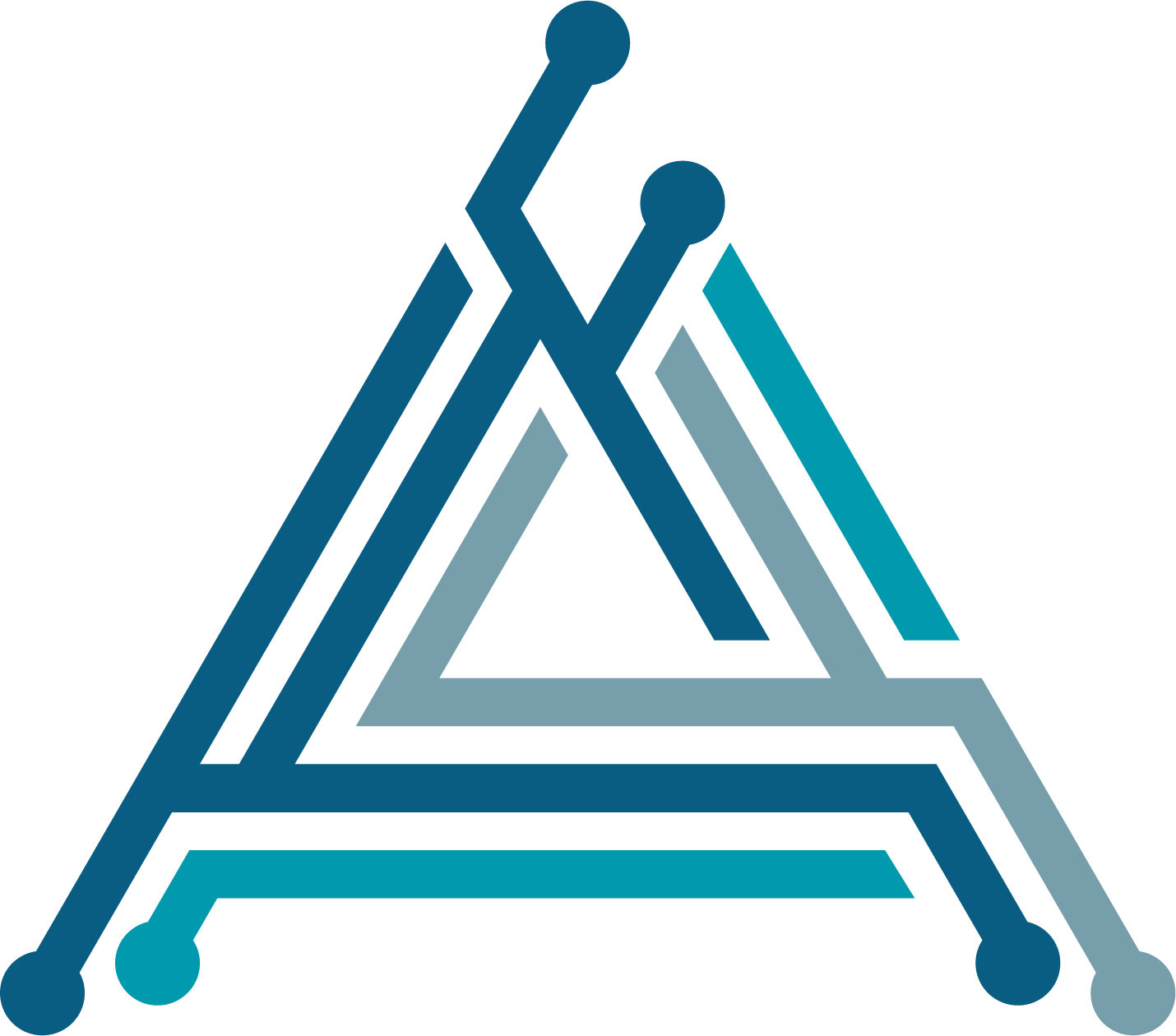
We Offer a Full Range of Printed Circuit Board Capabilities to Fit All of Your PCB Needs
AlteraFlex Circuits is a professional quick-turn PCB prototyping, PCB Assembly, and low-volume production manufacturer located in China.. The information below details some of the key capabilities that AlteraFlex Circuits can offer and support today. You will find information here relating to the specific materials we can support, the PCB technologies or product types that we currently produce, as well as some of the tolerances which we can achieve.
The first category is what we call "Quick-turn" and means we can offer Small Quantity - Quick Turn PCBs, Custom Spec - Standard PCBs,Quick-order PCB(Gerber Viewer).
The second is our “Advanced” offering and this shows the very best that AlteraFlex Circuits can offer: Full Spec PCBs, Highly Specialized Precision PCBs, & Large Scale Production, but sometimes some plates and materials are temporarily out of stock.
Please
send messages to your sales rep if your boards are beyond the capabilities listed below.
Smart Devices
We have large customer base in these industries. Customers choose us to make their PCBs in the prototype and production stage.
Medicine
We have large customer base in these industries. Customers choose us to make their PCBs in the prototype and production stage.
University, school and amateur
Students are our future scientists, we support them! Students and amateurs are price sensitive customers, our price guarantees they will rely on us for their PCB needs in terms of price and quality!
Commercial, industrial and automotive
Most of our customers are in these industries. Fast response, short delivery time, professional engineering support continuously affordable price help retain and expand customer scale in these industries.
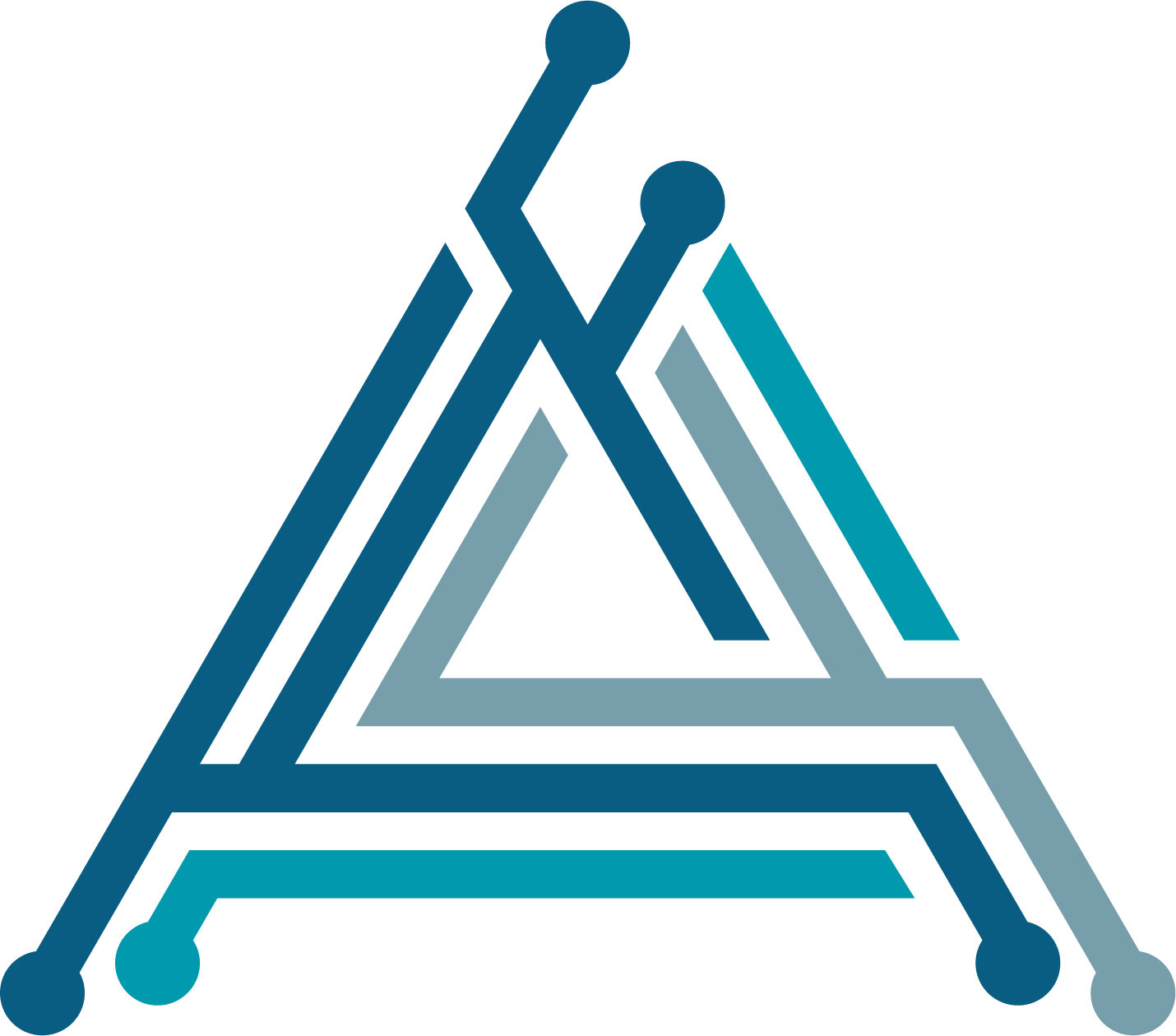
PCB Capabilities - Quick-Turn PCB
Items | Manufacturing Capabilities | Remarks |
---|---|---|
Number of Layers | 1-10 layers | For orders above 10 layers,please view the below "Standard PCB" or contact our sales rep. |
Material | FR-4,Aluminum | For Flex, Rigid-flex, Metal-based (Aluminum etc.,), HDI, Halogen-free, High Tg, etc.,please view the below "Standard PCB" or contact sales rep. |
Maximum PCB Size(Dimension) | 500*1100mm (min 5*6mm) | Any sizes beyond this dimension, please view the below "Standard PCB" or contact sales rep. |
Board Size Tolerance(Outline) | ±0.2mm/±0.5mm | ±0.2mm for CNC routing, and ±0.5mm for V-scoring. |
Board Thickness | 0.2-2.4mm | 0.2,0.4, 0.6, 0.8, 1.0, 1.2, 1.6, 2.0, 2.4mm. Please view the below "Standard PCB" or contact us if your board exceeds these. |
Board Thickness Tolerance(t≥1.0mm) | ±10% | Normally “+ Tolerance” will occur due to PCB processing steps such as electroless copper, solder mask and other types of finish on the surface. |
Board Thickness Tolerance(t<1.0mm) | ±0.1mm | Normally “+ Tolerance” will occur due to PCB processing steps such as electroless copper, solder mask and other types of finish on the surface. |
Min Trace | 0.1mm/4mil | Min manufacturable trace is 4mil(0.1mm), strongly suggest to design trace above 6mil(0.15mm) to save cost. |
Min Spacing | 0.1mm/4mil | Min manufacturable spacing is 4mil(0.1mm), strongly suggest to design spacing above 6mil(0.15mm) to save cost. |
Outer Layer Copper Thickness | 1oz/2oz/3oz(35μm/70μm/105μm) | Also known as copper weight. 35μm=1oz, 70μm=2oz, 105μm=3oz. Please view the below "Standard PCB" or contact us if you need copper weight greater than 3oz. |
Inner Layer Copper Thickness | 1oz/1.5oz(35μm/50μm) | Inner copper weight as per customer’s request for 4 and 6 layers(Multi-layer laminated structure). Please contact us if you need copper weight greater than 1.5oz. |
Drill Sizes (CNC) | 0.2-6.3mm | Min drill size is 0.2mm, max drill is 6.3mm. Any holes greater than 6.3mm or smaller than 0.3mm will be subject to extra charges. |
Min Width of Annular Ring | 0.15mm(6mil) | For pads with vias in the middle, Min width for Annular Ring is 0.15mm(6mil). |
Finished Hole Diameter (CNC) | 0.2mm-6.2mm | The finished hole diameter will be smaller than size of drill bits because of copper plating in the hole barrels |
Finished Hole Size Tolerance(CNC) | ±0.08mm | For example, if the drill size is 0.6mm, the finished hole diameter ranges from 0.52mm to 0.68mm will be considered acceptable. |
Solder Mask | LPI | Liquid Photo-Imageable is the mostly adopted. Thermosetting Ink is used in the inexpensive paper-based boards. |
Minimum Character Width(Legend) | 0.15mm | Characters of less than 0.15mm wide will be too narrow to be identifiable. |
Minimum Character Height (Legend) | 0.8mm | Characters of less than 0.8mm high will be too small to be recognizable. |
Character Width to Height Ratio (Legend) | 1:5 | In PCB silkscreen legends processing, 1:5 is the most suitable ratio |
Minimum Diameter of Plated Half Holes | 0.6mm | Design Half-Holes greater than 0.6mm to ensure better connection between boards. |
Surface Finishing | HASL with lead HASL lead free Immersion gold,OSP | The most popular three types of PCB surface finish. Please view the below "Standard PCB" or contact us for other finishes. |
Solder Mask | Green ,Red, Yellow, Blue, White ,Black | No extra charge (Green, Red, Yellow, Blue) |
Silkscreen | White, Black, None | No extra charge. |
Panelization | V-scoring, Tab-routing, Tab-routing with Perforation (Stamp Holes) | Leave min clearance of 1.6mm between boards for break-routing. For V-score panelization, set the space between boards to be zero. |
Others | Fly Probe Testing (Free) and A.O.I. testing(free), ISO 9001:2008 , IATF 16949, UL Certificate | No extra charge. |
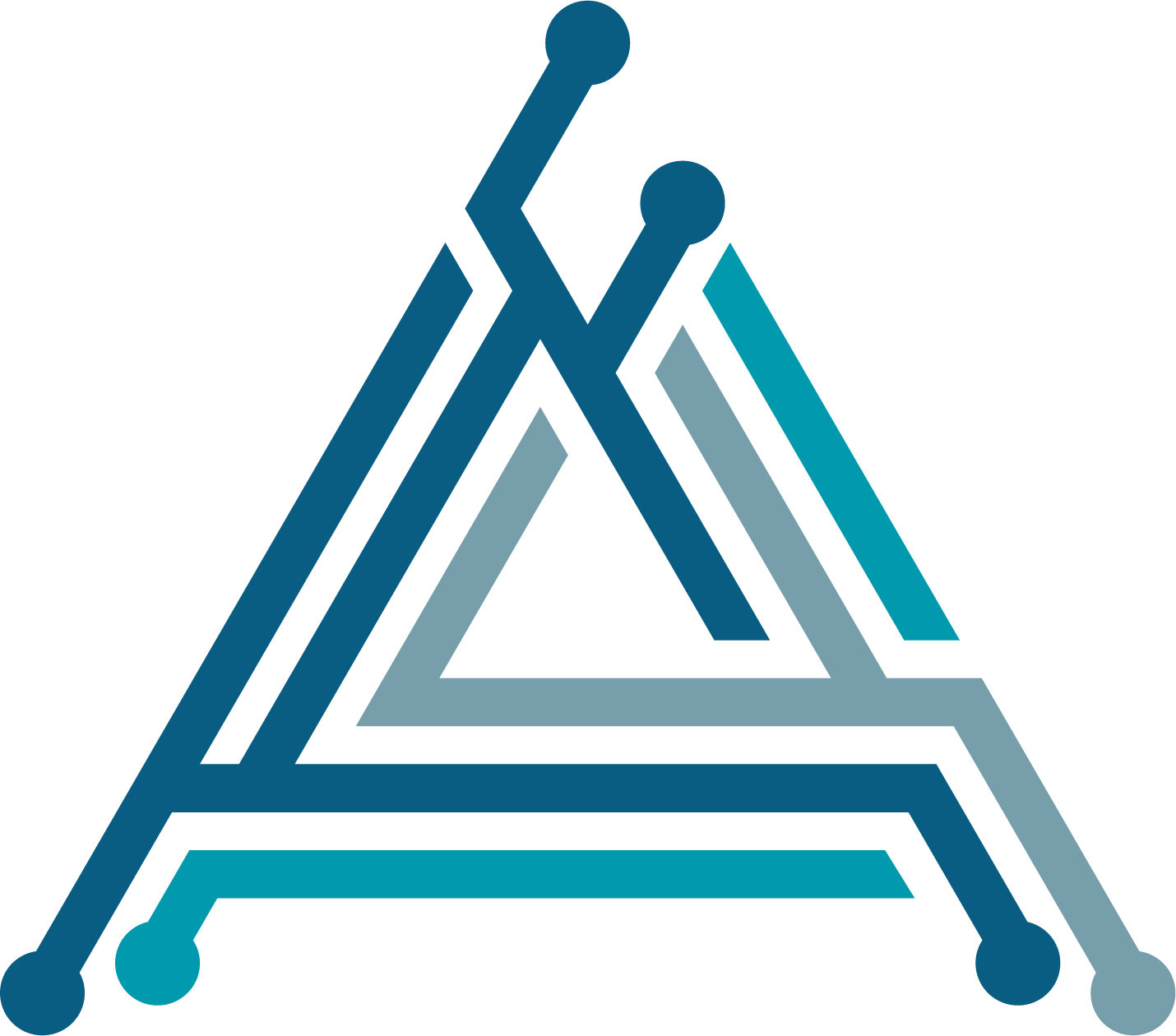
Advanced PCB Capabilities - Advanced PCB
Categories | No. | Items | Normal process | Medium difficulty | High difficulty (Non-standard review) | High difficulty (Unable to make) | Remarks |
---|---|---|---|---|---|---|---|
Product Type | 1 | Multilayer PCB Layers | |||||
2 | Blind and Buried Vias | Anylayer HDI | If meet the requirements of 2, 6, and 21 at the same time, it is classified as a high requirement product (thickness to diameter ratio, copper thickness of hole | ||||
3 | Surface Coating | Local immersion gold (long or short gold fingers, segmented gold finger craft) | Exceed this range require unconventional production processes | Partial immersion gold, thickness of gold or nickel reference to the thickness of the coating | |||
4 | Board Material | FR-4;aluminum,Rogers4 series + FR-4 mixed(The Prepreg is ShengYi brand and ROGERS4403 series);CEM-3、LianMao IT158/IT180A | Pure ROGERS4 series multi-layer board (Prepreg is 4450F),PTFE、aluminum+FR4、PTFE+FR4 | Exceed this range require unconventional production processes | Pure PTFE multi-layer board | Pure PTFE can’t be made because the lamination temperature isn’t up to standard,Can‘t laminate Rogers copper foil directly | |
Drills | 5 | Drill diameter | Nc drill | 0.20mm≤Drill diameter≤6.5mm More than 6.0mm using CNC milling hole diameter 0.2mm: maximum board thickness 1.6mm hole diameter diameter 0.25mm:maximum board thickness 2.0mm, hole diameter 0.3mm≤Ф≤0.35mm, maximum board thickness 3.2 mm, hole diameter 0.4mm≤Ф≤0.55mm, maximum board thickness 4.8 mm, hole diameter>0.55mm maximum board thickness 6.4 mm | 6.5mm or more ±0.1mm ≤ hole diameter tolerance (using CNC milling for 6.5mm or more) | The drill diameter more than 6.0mm, the hole diameter tolerance less than ±0.1mm. If exceed this range require unconventional production processes | Drill diameter below 0.2mm, and the aspect ratio≥10, which is medium difficulty | |
6 | Thickness to diameter ratio | Thickness to diameter ratio≤8 | 8 | 10 | Thickness to diameter ratio greater than 12 when the aperture cannot be compensated | If need to meet the requirement of 2, 6, and 21, it will be treat as high requirement product. | |
7 a. | countersink: Hole Diameter | 3.0mm≤hole diameter≤6.5mm | Unconventional production beyond this range | Countersink depth tolerance is controlled 0.15mm | |||
7 b. | countersink: Angle | 90° | Unconventional production beyond this range | Countersink depth tolerance is controlled 0.15m | |||
8 | Hole position tolerances | ±0.075mm | ±0.05mm | <+/-0.05mm | |||
9 a. | PTH | ±0.075mm or no customer requirements | ±0.05≤ hole diameter tolerance <±0.75mm | <±0.05mm | <+/-0.05mm | Metallized hole diameter tolerance of 6.0mm or more refers to the requirement of serial number 5 | |
9 b. | NPTH | ≥±0.075mm | <±0.05mm | <+/-0.025mm | Metallized hole diameter tolerance of 6.0mm or more refers to the requirement of serial number 5 | ||
10 a. | Hole to hole spacing (component hole) | ≥16MIL | 14≤Hole to hole spacing≤16 | 13≤Hole to hole spacing≤14 | <13mil | ||
10 b. | Hole to hole spacing (via(≤0.45mm)) | ≥11MIL | |||||
11 a. | Slot (Cut-out) Slot width | Plated slot ≥0.5mm Non-plated slot ≥0.8mm | More than 1.0mm, can be slot by machine | ||||
11 b. | Slot (Cut-out) Length to width ratio of slot | Length to width≥2 | Length to width<2 | ||||
12 a. | Castellated Holes diameter | ≥0.5mm | 0.5mm>diameter≥0.4mm | ||||
12 b. | Castellated Holes spacing (edge to edge) | ≥0.3mm | 0.3mm>diameters≥0.2mm | ||||
13 a. | 4L | ≥7MIL | 6MIL≤isolation ring, distance<7MIL | 5MIL≤isolation ring, distance<6MIL | If the size of one side is greater than 600MM, the inner hole to line and the hole to copper spacing must be greater than or equal to 15mil. If less than 15mil, it must be treated as unconventional review. The conventional process of 10 layers or more need to be incremented by 1 mil for each additional 2 layers. Change the isolation ring to 12mil or more as much as possible | ||
13 b. | 6L | ≥8MIL | 6.5MIL≤isolation ring, distance<8MIL | 6MIL≤isolation ring, distance<6.5MIL | If the size of one side is greater than 600MM, the inner hole to line and the hole to copper spacing must be greater than or equal to 15mil. If less than 15mil, it must be treated as unconventional review. The conventional process of 10 layers or more need to be incremented by 1 mil for each additional 2 layers. Change the isolation ring to 12mil or more as much as possible | ||
13 c. | 8L | ≥9MIL | 7MIL≤isolation ring, distance<9MIL | 6MIL≤isolation ring, distance<7MIL | If the size of one side is greater than 600MM, the inner hole to line and the hole to copper spacing must be greater than or equal to 15mil. If less than 15mil, it must be treated as unconventional review. The conventional process of 10 layers or more need to be incremented by 1 mil for each additional 2 layers. Change the isolation ring to 12mil or more as much as possible | ||
13 d. | ≥10L | ≥10MIL | 8MIL≤isolation ring, distance<10MIL<9MIL | 7MIL≤isolation ring, distance<8MIL | If the size of one side is greater than 600MM, the inner hole to line and the hole to copper spacing must be greater than or equal to 15mil. If less than 15mil, it must be treated as unconventional review. The conventional process of 10 layers or more need to be incremented by 1 mil for each additional 2 layers. Change the isolation ring to 12mil or more as much as possible | ||
Image Transfer | 14 a. | cooper thickness 18um | ≥4/4 mil | ≥4/3.5 mil | <3.5/3 mil | width/spacing | |
14 b. | cooper thickness 35um | ≥4/5 mil | ≥4/4 mil | <3.5/4 mil | width/spacing | ||
14 c. | cooper thickness 70um | ≥6/8mil | ≥6/7mil | <5/6 mil | width/spacing | ||
14 d. | cooper thickness 105um | ≥8/11 mil | ≥8/10 mil | <6/9 mil | width/spacing | ||
15 a. | cooper thickness 18um | ≥4/5 mil | ≥4/4 mil or parts 3.5/3.5mil | <3.5/3.5 mil | Local 3.5/3.5mil, only the distance from the GBA chip area line to the PAD | ||
15 b. | cooper thickness 35um | ≥5/6 mil | ≥5/5 mil | <4/4 mil |
Categories | No. | Items | Normal process | Medium difficulty | High difficulty (Non-standard review) | High difficulty (Unable to make) | Remarks |
---|---|---|---|---|---|---|---|
Product Type | 1 | Multilayer PCB Layers | 3L≤Layers≤16L | 18L≤Layers≤24L | ≥24L | ||
2 | Blind and Buried Vias | HDI(1+1+....+N+......+1+1) | Anylayer HDI | HDI(2+...+N...+2) | If meet the requirements of 2, 6, and 21 at the same time, it is classified as a high requirement product (thickness to diameter ratio, copper thickness of hole | ||
3 | Surface Coating | HASL(+gold finger),immersion gold, Immersion Gold +gold fingers with hard gold,OSP (+gold finger with hard gold), Immersion Tin (+gold finger with hard gold) (Not two different surface finish),Immersion Tin | Local immersion gold (long or short gold fingers, segmented gold finger craft) | Exceed this range require unconventional production processes | Partial immersion gold, thickness of gold or nickel reference to the thickness of the coating | ||
4 | Board Material | FR-4;aluminum,Rogers4 series + FR-4 mixed(The Prepreg is ShengYi brand and ROGERS4403 series);CEM-3、LianMao IT158/IT180A | Pure ROGERS4 series multi-layer board (Prepreg is 4450F),PTFE、aluminum+FR4、PTFE+FR4 | Exceed this range require unconventional production processes | Pure PTFE multi-layer board | Pure PTFE can’t be made because the lamination temperature isn’t up to standard,Can‘t laminate Rogers copper foil directly | |
Drills | 5 | Drill diameter | Nc drill | 0.20mm≤Drill diameter≤6.5mm More than 6.0mm using CNC milling hole diameter 0.2mm: maximum board thickness 1.6mm hole diameter diameter 0.25mm:maximum board thickness 2.0mm, hole diameter 0.3mm≤Ф≤0.35mm, maximum board thickness 3.2 mm, hole diameter 0.4mm≤Ф≤0.55mm, maximum board thickness 4.8 mm, hole diameter>0.55mm maximum board thickness 6.4 mm | 6.5mm or more ±0.1mm ≤ hole diameter tolerance (using CNC milling for 6.5mm or more) | The drill diameter more than 6.0mm, the hole diameter tolerance less than ±0.1mm. If exceed this range require unconventional production processes | Drill diameter below 0.2mm, and the aspect ratio≥10, which is medium difficulty | |
6 | Thickness to diameter ratio | Thickness to diameter ratio≤8 | 8 | 10 | Thickness to diameter ratio greater than 12 when the aperture cannot be compensated | If need to meet the requirement of 2, 6, and 21, it will be treat as high requirement product. | |
7 a. | countersink: Hole Diameter | 3.0mm≤hole diameter≤6.5mm | Unconventional production beyond this range | Countersink depth tolerance is controlled 0.15mm | |||
7 b. | countersink: Angle | 90° | Unconventional production beyond this range | Countersink depth tolerance is controlled 0.15m | |||
8 | Hole position tolerances | ±0.075mm | ±0.05mm | <+/-0.05mm | |||
9 a. | PTH | ±0.075mm or no customer requirements | ±0.05≤ hole diameter tolerance <±0.75mm | <±0.05mm | <+/-0.05mm | Metallized hole diameter tolerance of 6.0mm or more refers to the requirement of serial number 5 | |
9 b. | NPTH | ≥±0.075mm | <±0.05mm | <+/-0.025mm | Metallized hole diameter tolerance of 6.0mm or more refers to the requirement of serial number 5 | ||
10 a. | Hole to hole spacing (component hole) | ≥16MIL | 14≤Hole to hole spacing≤16 | 13≤Hole to hole spacing≤14 | <13mil | ||
10 b. | Hole to hole spacing (via(≤0.45mm)) | ≥11MIL | |||||
11 a. | Slot (Cut-out) Slot width | Plated slot ≥0.5mm Non-plated slot ≥0.8mm | More than 1.0mm, can be slot by machine | ||||
11 b. | Slot (Cut-out) Length to width ratio of slot | Length to width≥2 | Length to width<2 | ||||
12 a. | Castellated Holes diameter | ≥0.5mm | 0.5mm>diameter≥0.4mm | ||||
12 b. | Castellated Holes spacing (edge to edge) | ≥0.3mm | 0.3mm>diameters≥0.2mm | ||||
13 a. | 4L | ≥7MIL | 6MIL≤isolation ring, distance<7MIL | 5MIL≤isolation ring, distance<6MIL | If the size of one side is greater than 600MM, the inner hole to line and the hole to copper spacing must be greater than or equal to 15mil. If less than 15mil, it must be treated as unconventional review. The conventional process of 10 layers or more need to be incremented by 1 mil for each additional 2 layers. Change the isolation ring to 12mil or more as much as possible | ||
13 b. | 6L | ≥8MIL | 6.5MIL≤isolation ring, distance<8MIL | 6MIL≤isolation ring, distance<6.5MIL | If the size of one side is greater than 600MM, the inner hole to line and the hole to copper spacing must be greater than or equal to 15mil. If less than 15mil, it must be treated as unconventional review. The conventional process of 10 layers or more need to be incremented by 1 mil for each additional 2 layers. Change the isolation ring to 12mil or more as much as possible | ||
13 c. | 8L | ≥9MIL | 7MIL≤isolation ring, distance<9MIL | 6MIL≤isolation ring, distance<7MIL | If the size of one side is greater than 600MM, the inner hole to line and the hole to copper spacing must be greater than or equal to 15mil. If less than 15mil, it must be treated as unconventional review. The conventional process of 10 layers or more need to be incremented by 1 mil for each additional 2 layers. Change the isolation ring to 12mil or more as much as possible | ||
13 d. | ≥10L | ≥10MIL | 8MIL≤isolation ring, distance<10MIL<9MIL | 7MIL≤isolation ring, distance<8MIL | If the size of one side is greater than 600MM, the inner hole to line and the hole to copper spacing must be greater than or equal to 15mil. If less than 15mil, it must be treated as unconventional review. The conventional process of 10 layers or more need to be incremented by 1 mil for each additional 2 layers. Change the isolation ring to 12mil or more as much as possible | ||
Image Transfer | 14 a. | cooper thickness 18um | ≥4/4 mil | ≥4/3.5 mil | <3.5/3 mil | width/spacing | |
14 b. | cooper thickness 35um | ≥4/5 mil | ≥4/4 mil | <3.5/4 mil | width/spacing | ||
14 c. | cooper thickness 70um | ≥6/8mil | ≥6/7mil | <5/6 mil | width/spacing | ||
14 d. | cooper thickness 105um | ≥8/11 mil | ≥8/10 mil | <6/9 mil | width/spacing | ||
15 a. | cooper thickness 18um | ≥4/5 mil | ≥4/4 mil or parts 3.5/3.5mil | <3.5/3.5 mil | Local 3.5/3.5mil, only the distance from the GBA chip area line to the PAD | ||
15 b. | cooper thickness 35um | ≥5/6 mil | ≥5/5 mil | <4/4 mil | |||
15 c. | cooper thickness 70um | ≥7/8mil | ≥6/7mil | <5/6 mil | |||
15 d. | cooper thickness 105um | ≥10/12 mil | ≥8/10 mil | <6/9 mil |
Categories | No. | Items | Normal Process | Medium Difficulty | High difficulty (Non-standard review) | High difficulty (Unable to make) | Remarks |
---|---|---|---|---|---|---|---|
Image transfer | 16 a. | grid trace width/spacing cooper thickness 18um | ≥6/8 mil | <6/7 mil | |||
16 b. | grid trace width/spacing cooper thickness 35um | ≥8/10 mil | <8/9 mil | ||||
16 c. | grid trace width/spacing cooper thickness 70um | ≥11/13mil | ≥10/12mil | <10/11 mil | |||
16 d. | grid trace width/spacing cooper thickness 105um | ≥13/15 mil | ≥12/14 mil | <12/13 mil | |||
17 a. | cooper thickness 18um: via hole | ≥5mil | ≥4mil | <3 mil | |||
cooper thickness 18um: component hole | ≥8mil | ≥6mil | <6 mil | ||||
17 b. | cooper thickness 35um: via hole | ≥5mil | ≥4mil | <3 mil | |||
cooper thickness 35um: component hole | ≥10mil | ≥8mil | <8 mil | ||||
17 c. | cooper thickness 70um: via hole | ≥7mil | ≥6mil | <5 mil | |||
cooper thickness 70um: component hole | ≥12mil | ≥10mil | <10 mil | ||||
17 d. | cooper thickness 105um: via hole | ≥8mil | ≥6mil | <6 mil | |||
cooper thickness 105um: component hole | ≥14mil | ≥12mil | <12 mil | ||||
18 a. | width tolerance | width tolerance:≥±20% | ±10%≤ width tolerance:<±20% | <±10% | spacing must meet the requirements of 11 and 12, lf width is greater than 15mil, controlled by ±2.5mil | ||
18 b. | BGA pad diameter: hot air leveling (original) | ≥12MIL | ≥10MIL | <8mil | |||
BGA pad diameter: immersion gold (original) | diameter≥11mil | 8.0mil≤diameter<11.0mil | <6mil | ||||
19 a. | Line to board edge distance: CNC milling | 0.25mm | 0.20mm | <0.20mm | |||
19 b. | SMT width | ≥12mil | ≥9mil | <9mil以下 | <7mil,except the binding board | ||
Metal plating | 20 a. | Plating Thickness(µin) | Electroless Nickel-Immersion Gold,ENIG: Nickel thickness | 100-150 µin | 200 µin | |||
Plating Thickness(µin) | Electroless Nickel-Immersion Gold,ENIG: Gold Thickness | 1-8 µin | >8 µin | |||||
20 b. | Plating Thickness(µin) | Full board gold plating: Nickel thickness | 100-150 µin | 200-500 µin | ||||
Plating Thickness(µin) | Full board gold plating: Gold Thickness | 1-10 µin | 10-50 µin | >50 µin | Order center check the final price | |||
20 c. | Plating Thickness(µin) | Gold finger: Nickel thickness | 120-150 µin | 200-400 µin | Order center check the final price | |||
Plating Thickness(µin) | Gold finger: gold thickness | 1-30 µin | 30-50 µin | >50 µin | Order center check the final price | |||
21 a. | Hole copper thickness (µm): Through hole | 18-25 µm | 30-50 µm | >50 µm | If 2,6,19 is required to exist at the same time, it will be treated as high requirement. The thickness of the copper is 25-50UM, and the thickness of the copper is required to be 2-3OZ generally. | ||
21 b. | Hole copper thickness (µm): Blind hole (mechanical hole) | 18-25 µm | 30-50 µm | >50 µm | If 2,6,19 is required to exist at the same time, it will be treated as high requirement. The thickness of the copper is 25-50UM, and the thickness of the copper is required to be 2-3OZ generally. | ||
21 c. | Hole copper thickness (µm): Buried hole | 15-25 µm | 30-50 µm | >50 µm | If 2,6,19 is required to exist at the same time, it will be treated as high requirement. The thickness of the copper is 25-50UM, and the thickness of the copper is required to be 2-3OZ generally. |
Categories | No. | Items | Normal process | Medium difficulty | High difficulty (Non-standard review) | High difficulty (Unable to make) | Remarks |
---|---|---|---|---|---|---|---|
Metal plating | 22 a. | BOTTOM COPPER THICKNESS Inner and outer copper thickness (OZ) | 0.5-4 | 4-6 | >6 | ||
23 b. | SOLDER MASK green solder mask Bridge (mil): cooper thicknesss<2OZ | 4(spacing between ICs is 8 mil, green oil,variegated or black oil≥4.5mil | 3-4(spacing between ICs is 7-8 mil, green oil,variegated or black oil≥4mil | ||||
23 c. | SOLDER MASK green solder mask Bridge (mil): cooper thicknesss<2OZ | 5 | 4 | ||||
23 d. | SOLDER MASK Plug Hole Diameter | 0.20mm≤hole diameter≤0.40mm,plug hole fullness 70% | 0.4mm< hole diameter ≤0.70mm | fullness 100% | |||
23 e. | SOLDER MASK Plug Hole Board Thickness | 0.40mm≤board thickness≤2.4mm | >2.4MM | ||||
24 | solder mask color | Green, matt green, blue, red, black, matte black, white, yellow | Special colors need to be purchased or deployed in advance | ||||
silkscreen | 25 a. | ETCHED SILKSCREEN (FINISHED COPPER THICKNESS) Copper thickness 18um word width/word height | 8MIL/40MIL | 7MIL/35MIL | |||
25 b. | ETCHED SILKSCREEN (FINISHED COPPER THICKNESS) Copper thickness 35um word width/word height | 9MIL/40MIL | 8MIL/35MIL | ||||
25 c. | ETCHED SILKSCREEN (FINISHED COPPER THICKNESS) Copper thickness 75um word width/word height | 12MIL/60MIL | 10MIL/50MIL | ||||
25 d. | ETCHED SILKSCREEN (FINISHED COPPER THICKNESS) Copper thickness 105um word width/word height | 16MIL/60MIL | 14MIL/50MIL | ||||
Outline | 26 a. | MAXIMUM BOARD THICKNESS Double PCB | 3.2MM | 4.5MM | >4.5MM | calculated by 4 layers if the thickness more than 3mm | |
26 b. | MAXIMUM BOARD THICKNESS Multilayer layer board | 3.2MM | 4.5MM | >4.5MM | |||
27 a. | Minimum board thickness (single and double panel refers to substrate thickness) Single or Double side PCB (pcb prototype) | ≥0.3mm | 0.25mm | ||||
27 b. | Minimum board thickness (single and double panel refers to substrate thickness) 4L | ≥0.60mm | 0.40mm | <0.40mm | |||
27 c. | Minimum board thickness (single and double panel refers to substrate thickness) 6L | ≥0.9mm | 0.70mm | <0.70mm | |||
27 d. | Minimum board thickness (single and double panel refers to substrate thickness) 8L | ≥1.20mm | 1.00mm | <1.00mm | |||
27 e. | Minimum board thickness (single and double panel refers to substrate thickness) 10L | ≥1.40mm | 1.20mm | <1.20mm | |||
27 f. | Minimum board thickness (single and double panel refers to substrate thickness) 12L | ≥1.70mm | 1.50mm | <1.50mm | |||
27 g. | Minimum board thickness (single and double panel refers to substrate thickness) 14L | ≥2.00mm | 1.80mm | <1.80mm | |||
28 a. | thickness (T) tolerance MM (multilayer layer pcb) T≤1.0 | ±0.10 | Need to review if less than the tolerance | If the tolerance is unilateral tolerance, the tolerance shall be double tolerance value, such as: 1.8mm requires positive tolerance, the tolerance shall be 0-0.36mm | |||
28 b. | thickness (T) tolerance MM (multilayer layer pcb) 1.0 | ±0.13 | Need to review if less than the tolerance | If the tolerance is unilateral tolerance, the tolerance shall be double tolerance value, such as: 1.8mm requires positive tolerance, the tolerance shall be 0-0.36mm | |||
28 c. | thickness (T) tolerance MM (multilayer layer pcb) 1.6 | ±0.18 | Need to review if less than the tolerance | If the tolerance is unilateral tolerance, the tolerance shall be double tolerance value, such as: 1.8mm requires positive tolerance, the tolerance shall be 0-0.36mm | |||
28 d. | thickness (T) tolerance MM (multilayer layer pcb) 2.5 | ±0.23 | Need to review if less than the tolerance | If the tolerance is unilateral tolerance, the tolerance shall be double tolerance value, such as: 1.8mm requires positive tolerance, the tolerance shall be 0-0.36mm | |||
28 e. | thickness (T) tolerance MM (multilayer layer pcb) T≥3.2 | ±8% | Need to review if less than the tolerance | If the tolerance is unilateral tolerance, the tolerance shall be double tolerance value, such as: 1.8mm requires positive tolerance, the tolerance shall be 0-0.36mm |
Categories | No. | Items | Normal process | Medium difficulty | High difficulty (Non-standard review) | High difficulty (Unable to make) | Remarks |
---|---|---|---|---|---|---|---|
Outline | 29 a. | Maximum finished board size Single and double side PCB | 508×610mm | Beyond this range needs to be reviewed | |||
29 b. | Maximum finished board size Multilayer Layer PCB | 508×600mm | Beyond this range needs to be reviewed | ||||
30 | Minimum finished pcb size | ≥20mm | 10mm≤Size<20mm | <10mm | |||
31 a. | BEVELING FOR GOLD FINGER Bevel angle | 20°30°45°60° | <20°Or>60° | ||||
31 b. | BEVELING FOR GOLD FINGER Bevel angle tolerance | >±5° | ±5° | <±5° | |||
31 c. | BEVELING FOR GOLD FINGER Bevel depth tolerance | tolerance≥±0.15mm | ±0.15mm< Tolerance ≤ ±0.1mm | tolerance<±0.10mm | |||
32 | Shape tolerance | tolerance≥±0.15mm | ±0.10mm≤tolerance<±0.15mm | Tolerance<±0.10mm or more than two form tolerance control | |||
33 a. | V-CUT Angle | 20°30°45°60° | |||||
33 b. | V-CUT The Maximum number of V-CUT | In 20 times | In 30 times | In 40 times | |||
33 c. | V-CUT Width of the shape | 80MM< width <560MM | 60MM< width <80MM | width <60MM | |||
33 d. | V-CUT board thickness | 0.6MM≦thickness≦2.4MM | 0.5MM≦thickness<0.6MM | thickness<0.5MM or thickness>2.4MM | below 0.5mm is single-sided V-CUT | ||
33 e. | V-CUT Remaining thickness | ≥0.25MM | <0.25MM | ||||
33 f. | Conventional V-CUTT、V-CUT: Skip V-CUT | ||||||
34 a. | PANEL SIZE The minimum panel size | ≥100*120mm | \ | <100*120mm | The thickness of the finished board is less than 0.4MM, the panel size can’t exceed 14inch, and the maximum size of the HASL PCB can’t exceed 24inch | ||
34 b. | PANEL SIZE The Maximum panel size | ≤20*24 inch | \ | Need to review if beyond range | The thickness of the finished board is less than 0.4MM, the panel size can’t exceed 14inch, and the maximum size of the HASL PCB can’t exceed 24inc | ||
35 a. | Impedance control tolerance | ±10%,50Ω and below:±5Ω | \ | <±10%,50Ω and below <±5Ω | |||
35 b. | bow and twist tolerance | bow and twist≤0.75% | 0.75%≤bow and twist≤0.5% | bow and twist<0.5% | asymmetry boards bow and twist tolerance 1.2% | ||
36 a. | HASL processing capacity component hole diameter | hole diameter>0.5mm | 0.4mm≤hole diameter≤0.5mm | ||||
36 b. | HASL processing capacity board thickness | 0.5mm≤board thickness≤3.5mm | 0.4mm≤board thickness<0.5mm | ||||
36 c. | HASL processing capacity thickness | 2um≤thickness of Tin≤30um | |||||
37 | Acceptance Criteria IPC standard | IPC2 level standard | IPC Level 3 standard |