BGA Assembly Capabilities
Ball Grid Array (BGA) is an important type of surface mount packaging employed in integrated circuit boards. BGAs are mainly used for mounting high-performance devices including microprocessors. There are several BGA assembly service providers who offer these packages with different specifications. We have immense experience and expertise in designing Ball Grid Array Assembly (BGA) packages. Equipped with advanced manufacturing and inspection equipment, we can produce high-quality BGA circuit boards with excellent yield rates.
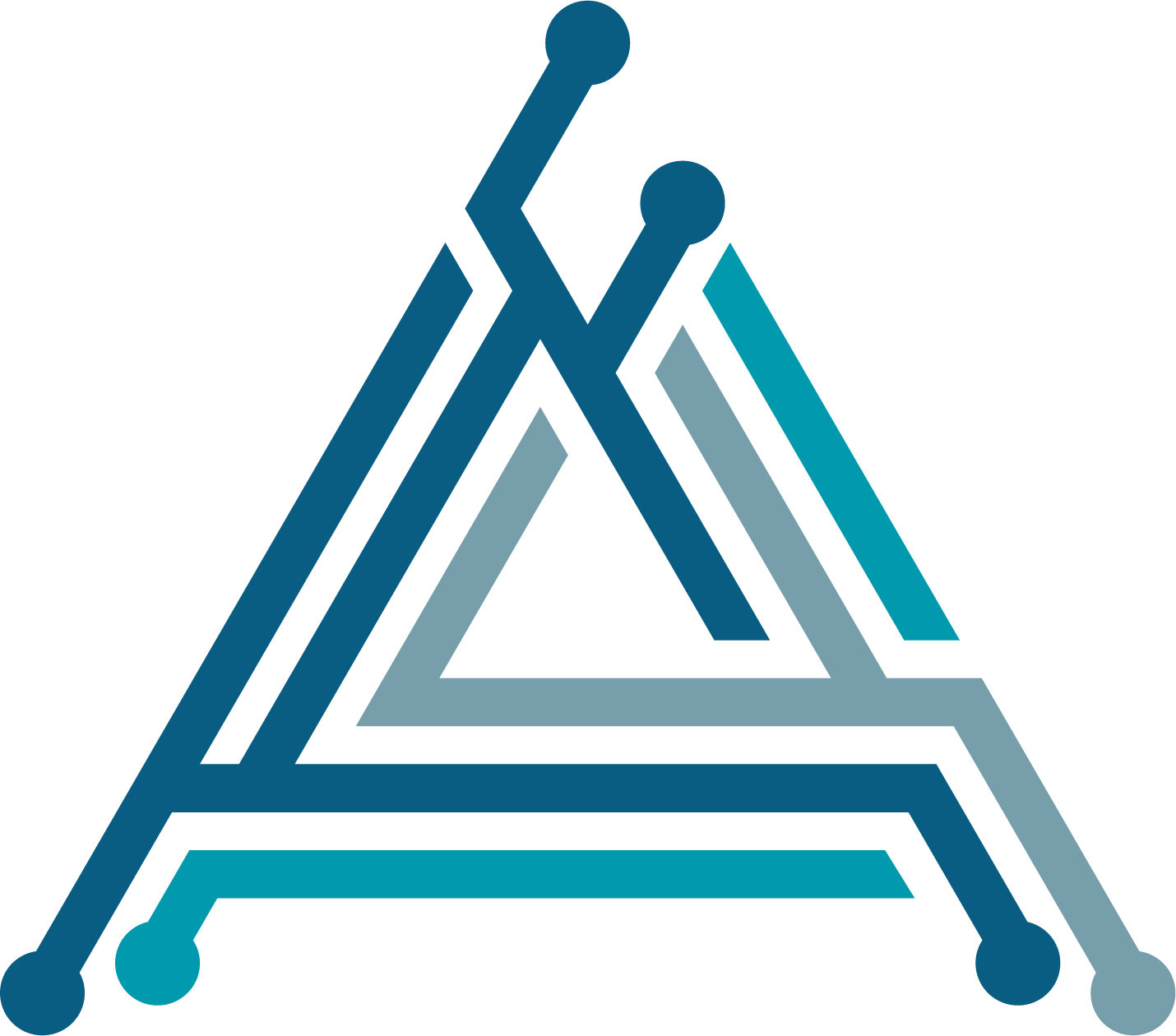
What is BGA?
A ball grid array (BGA) is a type of surface-mount packaging (a chip carrier) used for integrated circuits. BGA packages are used to permanently mount devices such as microprocessors. A BGA can provide more interconnection pins than can be put on a dual in-line or flat package.
The whole bottom surface of the device can be used, instead of just the perimeter. The traces connecting the package's leads to the wires or balls which connect the die to package are also on average shorter than with a perimeter-only type, leading to better performance at high speeds .[citation needed].
Soldering of BGA devices requires precise control and is usually done by automated processes.
Advantages:
Ball Grid Array (BGA) style circuit boards, which used small circular balls of solder to allow the flow of electricity between parts of the circuit.
Higher-density circuits: As through-hole circuits were more densely-populated, soldering them accurately without crossover or short-circuits became nearly impossible.
Heat conduction: BGA circuits allow heat to pass much more easily from the integrated circuit outwards, reducing overheating problems.
Lower inductance: Because each solder ball in a BGA circuit is generally only a handful of millimeters large, problems from interference within the circuit are greatly minimized.
AlteraFlex BGA Assembly Capabilities:
The usually BGA technology of AlteraFlex are minimum size 0.35mm, the minimum distance to circuit line is 0.2mm,the minimum distance between two BGA is 0.2mm. If you need higher requirement, please make a note.
Four automated placement systems available with Vision Systems capable of inspecting solder ball coverage.
One automated system available with a 3-D laser capable of inspecting solder ball height Automatic placement of CBGA, PBGA, and MBGA
Verification of BGA’s using Phoenix real-time x-ray system.
Have Questions?
If you have any questions or need any further information, please feel free to contact your dedicated customer service.