PCB Ball Grid Array (BGA)
Ball Grid Array (BGA) is an important type of surface mount packaging employed in integrated circuit boards. BGAs are mainly used for mounting high performance devices including microprocessors. There are several BGA assembly service providers who offer these packages in different specifications. Sierra Assembly stands tall among them. We have immense experience and expertise in designing Ball Grid Array Assembly (BGA) packages. Equipped with advanced manufacturing and inspection equipment, we can produce high quality BGA circuit boards with excellent yield rates.
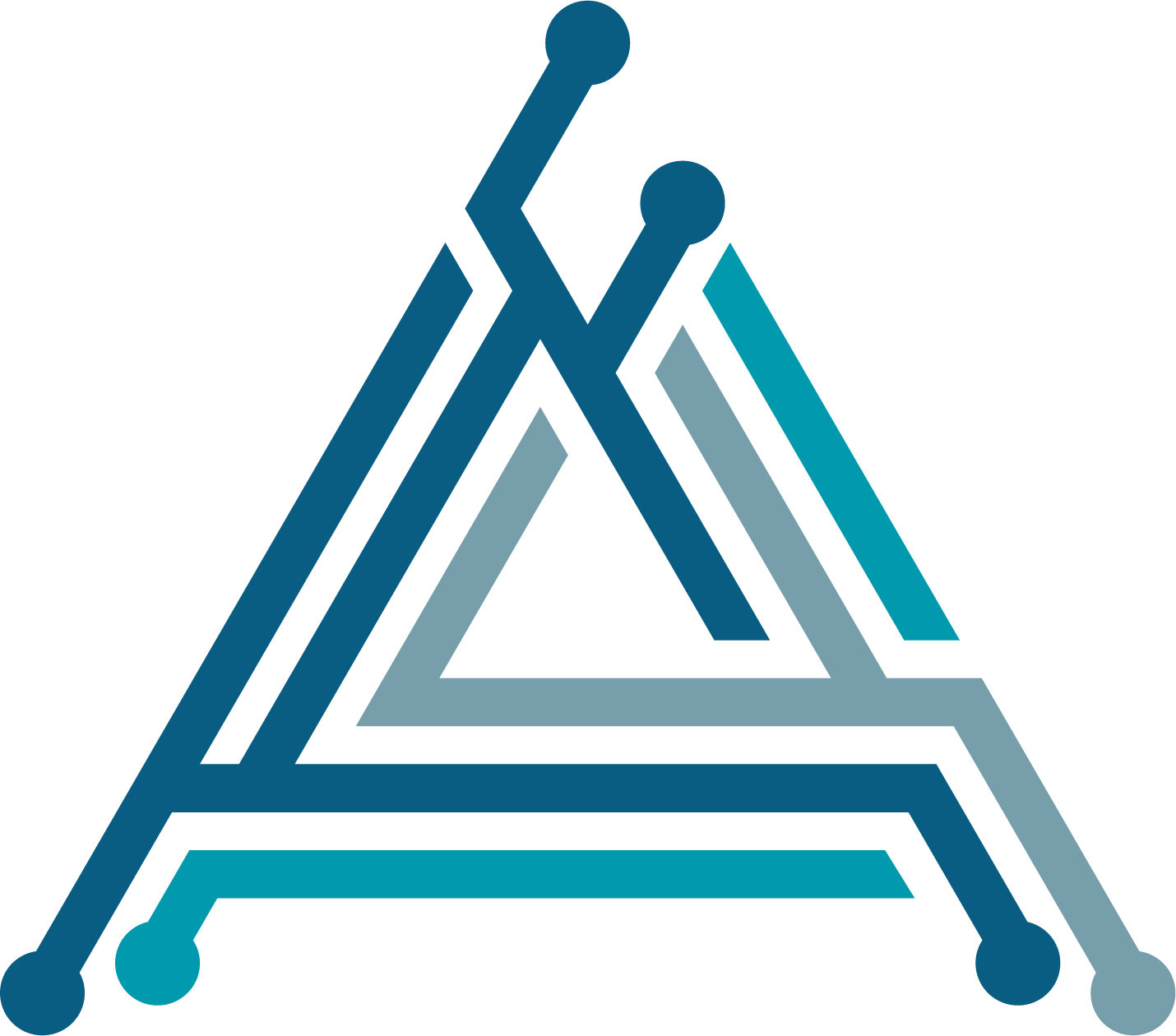
PCB BGA
The leads are also on average shorter than with a perimeter-only type, leading to better performance at high speeds. Soldering of BGA devices requires precise control and is usually done by automated processes. BGA devices are not suitable for socket mounting.
AlteraFlex BGA technology:
According to our prototype factory's production capability, the diameter of BGA pad (round one below) should be at least 0.25mm, the space between copper trace and BGA PAD should be at least 0.15mm, BGA to Pad should be not less 0.15mm(1OZ complete copper thickness),BGA Pad to BGA Pad should be not less 0.35mm.
AlteraFlex advanced PCB factory can now manufacturing abilities:
The minimum diameter of BGA is 0.2MM (the sample limit can be 0.15MM), the minimum BGA to line is 3MIL (the prototype limit can be 2.5MIL), the BGA spacing limit is 0.4mm, and the conventional 0.5mm Challenges to the limit are not easy to produce, because the scrap rate is too high, resulting in increased costs.
The Advantage of BGA:
Have Questions?
If you have any questions or need any further information, please feel free to contact your dedicated customer service.